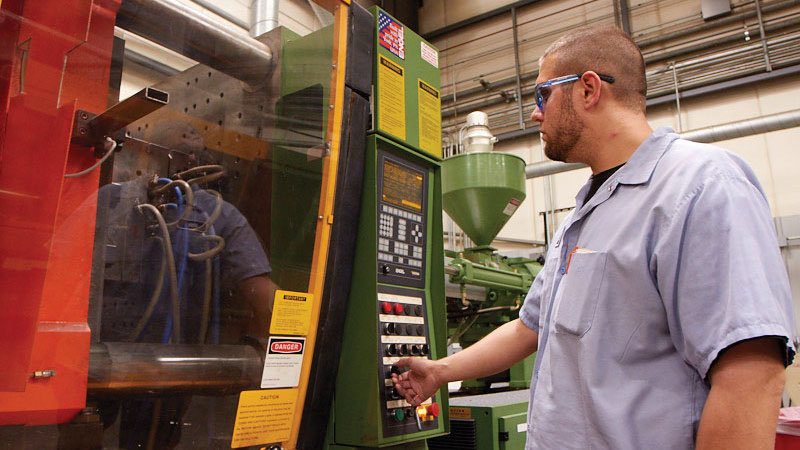
Polyurethane Injection Molding
A molding method that involves a high filling pressure and an automated process
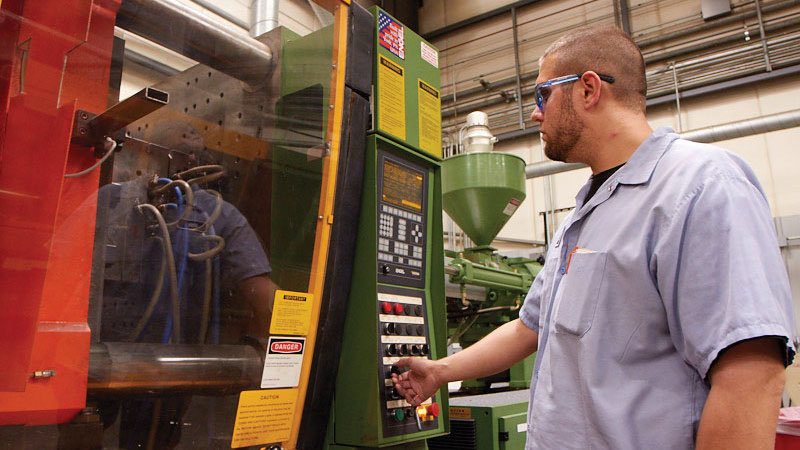
Polyurethane Injection Molding
A molding method that involves a high filling pressure and an automated process
Why It Matters
Molten polyurethane is injected into a closed mold at high pressure. The high-pressure forces the polyurethane to completely fill the mold cavity. The resulting product is net shape, or near net shape, directly out of the mold.
Injection molding is traditionally thought of for high-volume production. But our polyurethane injection molding capabilities also support low- and mid-volume production quantities.
The Gallagher Advantage
Our injection molding operation is optimized for producing high-quality, complex products.
What makes a complex product? Your product may be complex if it requires: bonding to an insert, multiple injected materials, large product size, and/or both thick and thin cross-sectional areas. We do all these.
We also have various sizes of injection molding machines to accommodate small to large product sizes.
How We Do It
Injection molding is a repetitive process with a fast cycle time on the order of seconds. The entire process takes place in one specialized, automated injection molding machine. It starts with feeding solid polyurethane pellets into the machine’s injecting barrel. The barrel contains a reciprocating screw that pushes the pellets forward toward the mold. The high shear action of the screw frictionally heats the pellets, fully melting them by the end of the barrel. When enough material has accumulated at the end of the barrel, the molten polyurethane is forced at high pressure and velocity into the mold in one shot.
The material enters the mold through a series of channels, called gates. The gates are specially designed so that the mold cavity is fully filled in a short time. The mold also incorporates cooling lines to reduce the time required for the molten material to solidify in the mold. Once the material has solidified, the mold is opened and the product is ejected using an array of pins, sleeves, and strippers.
Meanwhile, enough molten polyurethane has accumulated in the barrel for the next shot in order to start the molding cycle over again.
Materials To Meet Your Application
Our thermoplastic polyurethanes cover a wide range of performance properties. We customize the formulation of our polyurethanes to meet the specific requirements of each project. Tell us about your application and we’ll guide you through your best material options.