Custom Polyurethane Molding Services
We collaboratively design, precisely mold, and dependably deliver
polyurethane components that improve your product’s performance
Countless applications because of three key advantages
Polyurethanes have outstanding abrasion resistance, often outwearing corresponding parts made of metal, plastic, or rubber by a wide margin.
Polyurethanes have an excellent load-bearing capability and exhibit deflection and recovery that far exceed plastic or metal.
Creating complex shapes is no problem for polyurethane because we mold it in its liquid state. Polyurethane can be permanently attached — or bonded — to metals, plastics, and composites during the molding process.
Performance properties tailored to your application
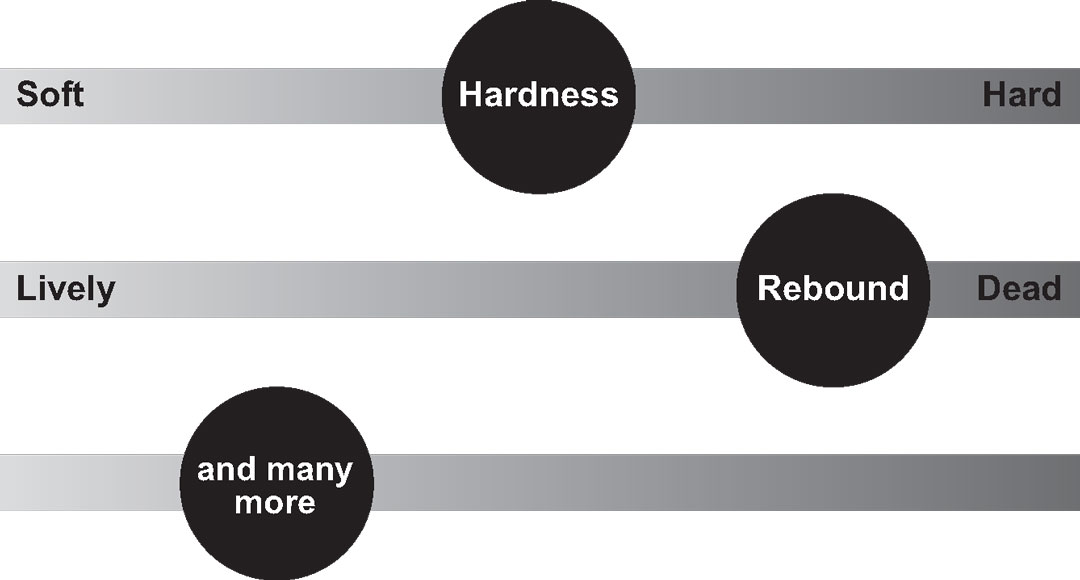
We formulate the polyurethane to match your requirements. What can we customize for you?
Countless applications because of three key advantages
Polyurethanes have outstanding abrasion resistance, often outwearing corresponding parts made of metal, plastic, or rubber by a wide margin.
Polyurethanes have an excellent load-bearing capability and exhibit deflection and recovery that far exceed plastic or metal.
Creating complex shapes is no problem for polyurethane because we mold it in its liquid state. Polyurethane can be permanently attached — or bonded — to metals, plastics, and composites during the molding process.
Performance properties tailored to your application
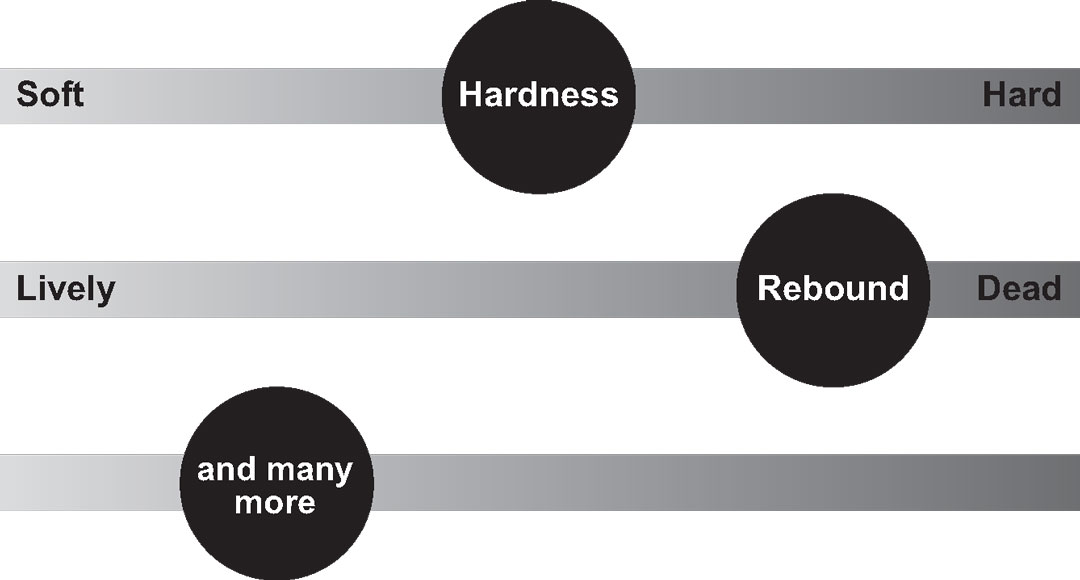
We formulate the polyurethane to match your requirements. What can we customize for you?
You’ll Succeed With Us
Disrupting industries… It’s in our DNA
The beginning of our custom polyurethane molding services:
Starting with a Golf Ball
The first golf ball was an improvised pebble. From there, its construction advanced to using beech wood, then leather, then tree sap. Now the golf ball is a high-tech combination of core and cover.
Today’s best golf balls use an extremely durable polyurethane cover. Compared to other materials, polyurethane provides higher spin rates, better control, and a softer feel. It delivers performance that would have been unimaginable back in golf’s early days.
Golfers can thank Richard (Dick) Gallagher. Dick was the inventor of the polyurethane golf ball cover.
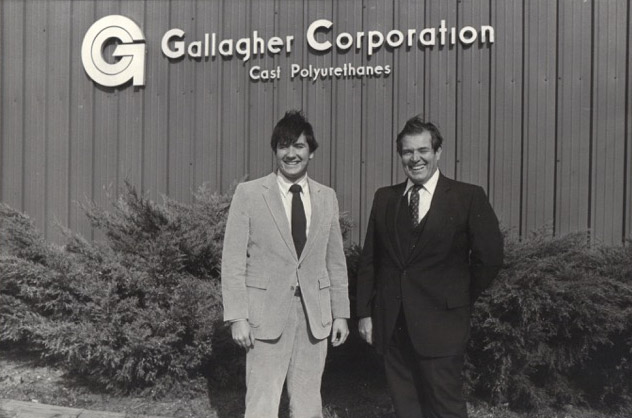
A Dream is Born
As a DuPont chemist, Dick developed and commercialized the earliest cast polyurethane materials. After the patent of the golf ball cover, he became more intrigued by the untapped potential of polyurethane to disrupt products. In 1965, Dick founded Gallagher Corporation to provide custom urethane molding services.
His mission: Mold polyurethane into game-changing products for OEMs across all industries.
Following Through on the Mission
Many new faces, and two more Gallagher generations, have joined the team. Today, we support hundreds of OEMs with our custom polyurethane molding services and products, across a variety of industries.
Our strategy remains the same — leverage the advantages of polyurethane to provide longer lasting and higher performing products that change industries.
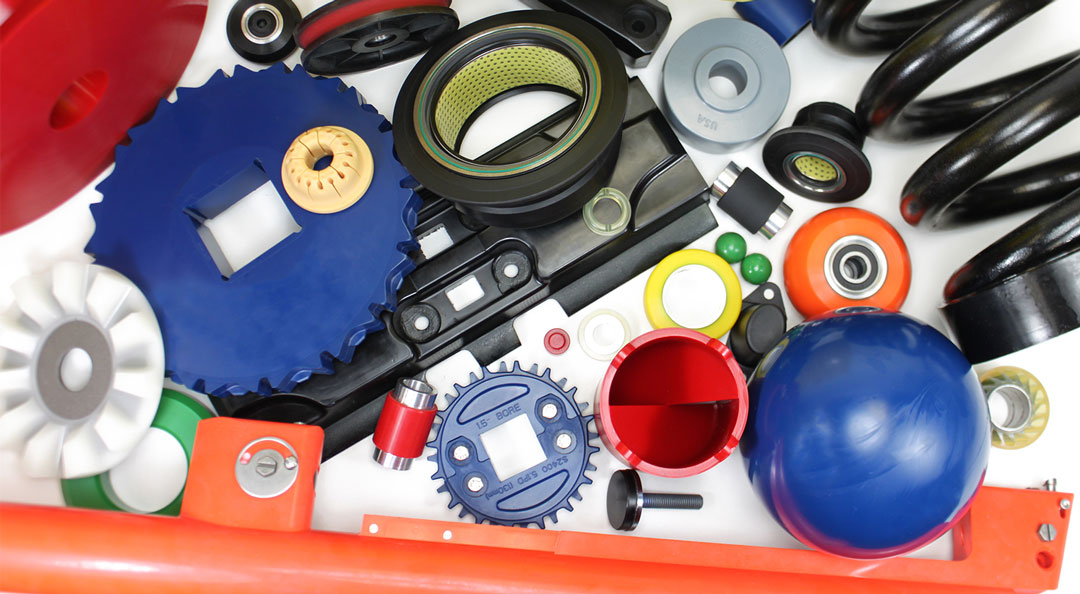
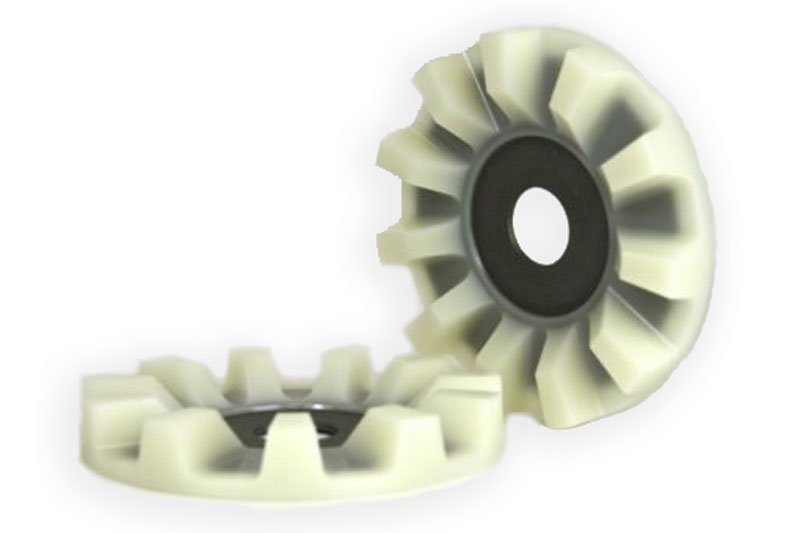
Case in Point: the John Deere Cotton Doffer
The doffer is one of two critical components that work together to pick cotton. First, barbed spindles rotate at high speed to remove the seed-cotton from the plant. Then, counter-rotating doffers pull the seed-cotton off of the spindles. It is a tough job subject to abrasive field conditions.
The problem John Deere faced was two-fold. First, the rubber doffers wore too quickly. Second, the black fragments that wore off the rubber doffers contaminated the white cotton harvest.
We worked with John Deere to understand the doffer application. Then we went to work on a custom polyurethane formulation to match their requirements. There were prototypes, field tests, and more prototypes. In the end, we significantly improved doffer wear life and eliminated the black rubber contamination. Our polyurethane doffer has been the industry standard for the past 30 years.
But it’s not about us. We’re happy to have made a contribution to John Deere’s market leadership.
How can we help you change your industry?
The Only Thing
More Amazing Than Polyurethane
Is How You Use It
We collaboratively design, precisely
mold, and dependably deliver
polyurethane components that improve
your products performance
Countless applications because of three key advantages
Polyurethanes have outstanding abrasion resistance, often outwearing corresponding parts made of metal, plastic, or rubber by a wide margin.
Polyurethanes have an excellent load-bearing capability and exhibit deflection and recovery that far exceed plastic or metal.
Creating complex shapes is no problem for polyurethane because we mold it in its liquid state. Polyurethane can be permanently attached — or bonded — to metals, plastics, and composites during the molding process.
Performance properties tailored to your application
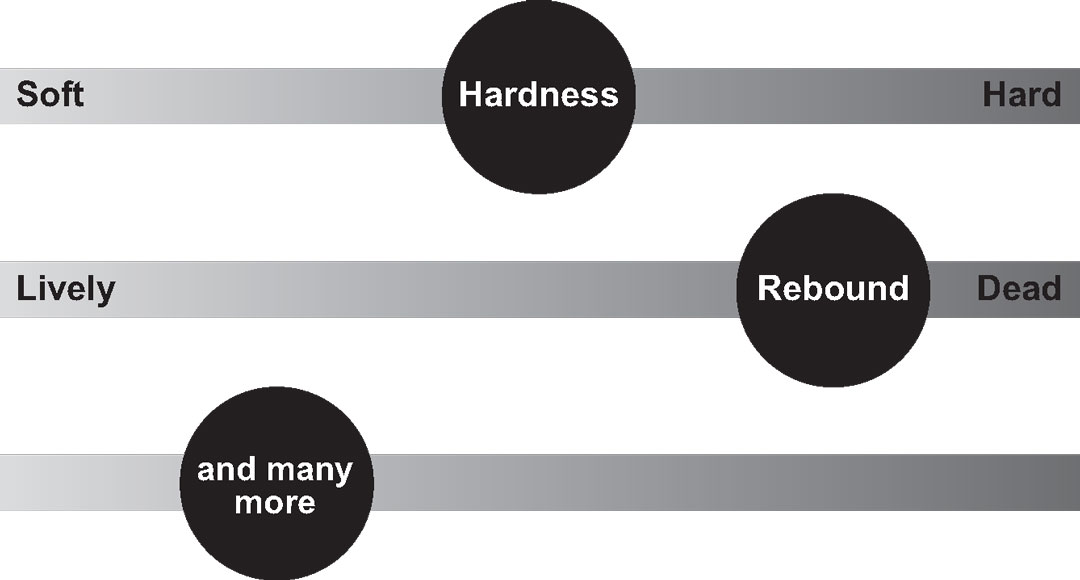
We formulate the polyurethane to match your requirements. What can we customize for you?
You’ll succeed with us
WE ARE EXPERTS
We unlock the potential of polyurethane to solve your challenges
Learn More ›
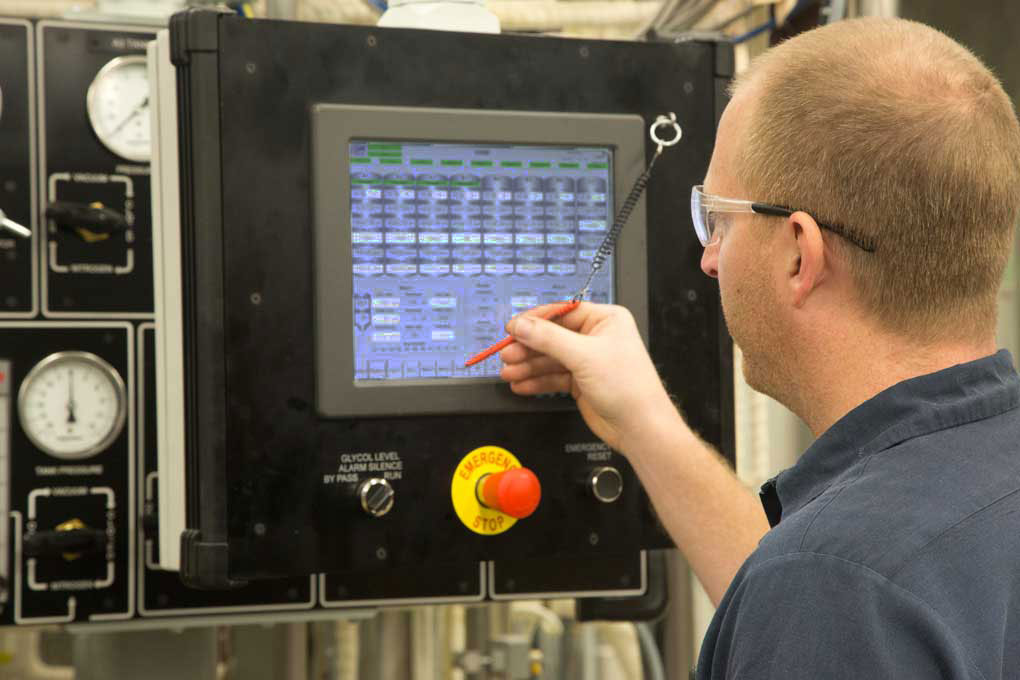
WE DELIVER
Superior products, dependably delivered
Learn More ›
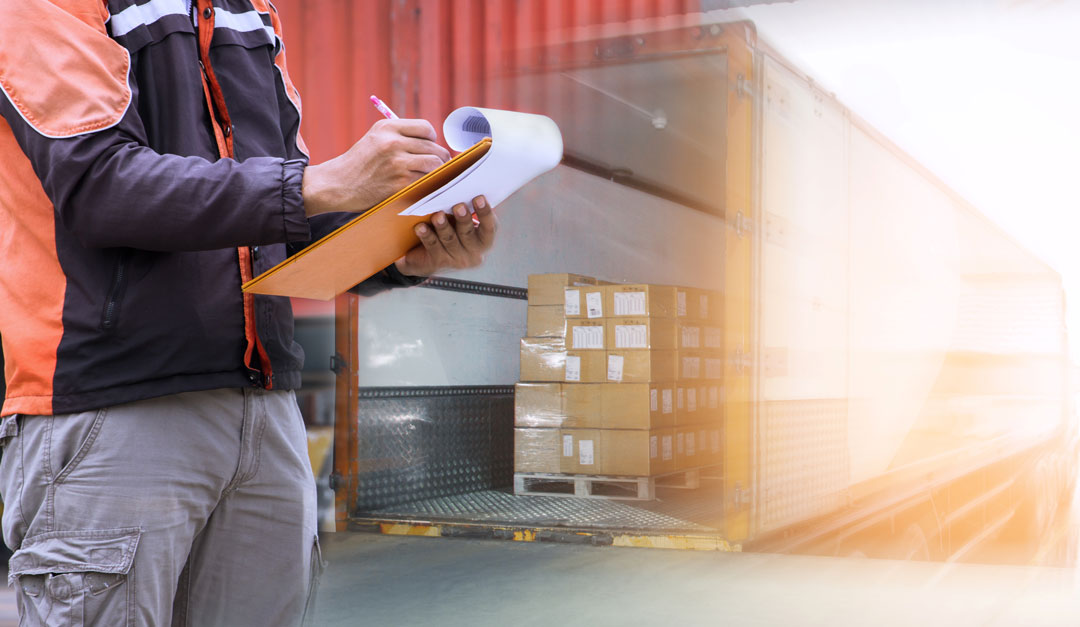
WE ARE PARTNERS
Together we’ll achieve success
Learn More ›
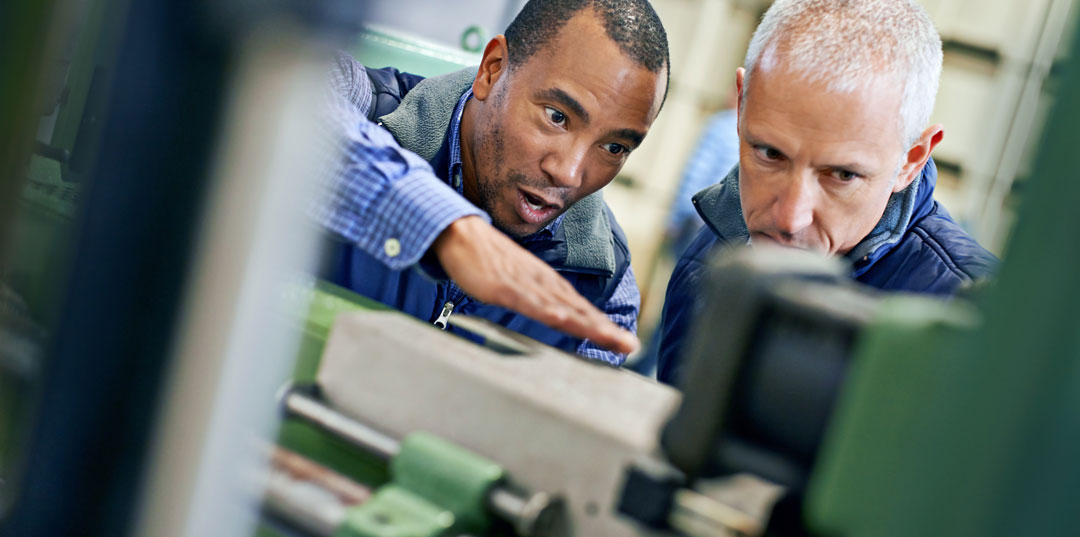
Disrupting industries… It’s in our DNA
Starting with a Golf Ball
Oh, how the golf ball has evolved… Some say that the first golf ball was an improvised pebble. From there, its construction advanced to using beech wood, then leather, then tree sap. Now the golf ball is a high-tech combination of core and cover.
Today’s best golf balls use an extremely durable polyurethane cover. Compared to other materials, polyurethane provides higher spin rates, better control, and a softer feel. It delivers performance that would have been unimaginable back in golf’s early days.
Golfers can thank Richard (Dick) Gallagher. Dick was the inventor of the polyurethane golf ball cover.
A Dream is Born
As a DuPont chemist, Dick developed and commercialized the earliest cast polyurethane materials. After the patent of the golf ball cover, he became more intrigued by the untapped potential of polyurethane to disrupt products. In 1965, Dick founded Gallagher Corporation to design and manufacture custom polyurethane products.
His mission: Mold polyurethane into game-changing products for OEMs across all industries.
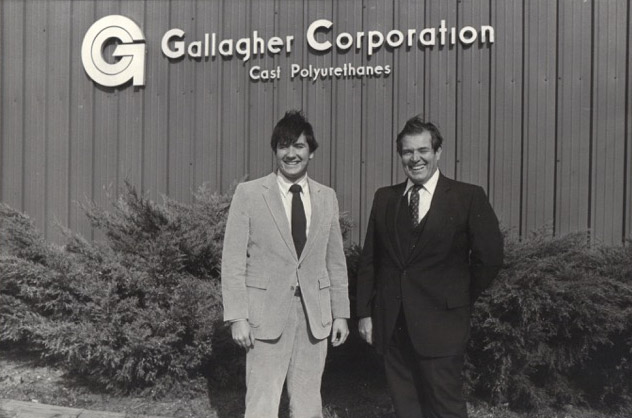
Following Through on the Mission
Many new faces, and two more Gallagher generations, have joined the team. Today, we support hundreds of OEMs with our custom polyurethane products, across a variety of industries.
Our strategy remains the same — leverage the advantages of polyurethane to provide longer lasting and higher performing products that change industries.
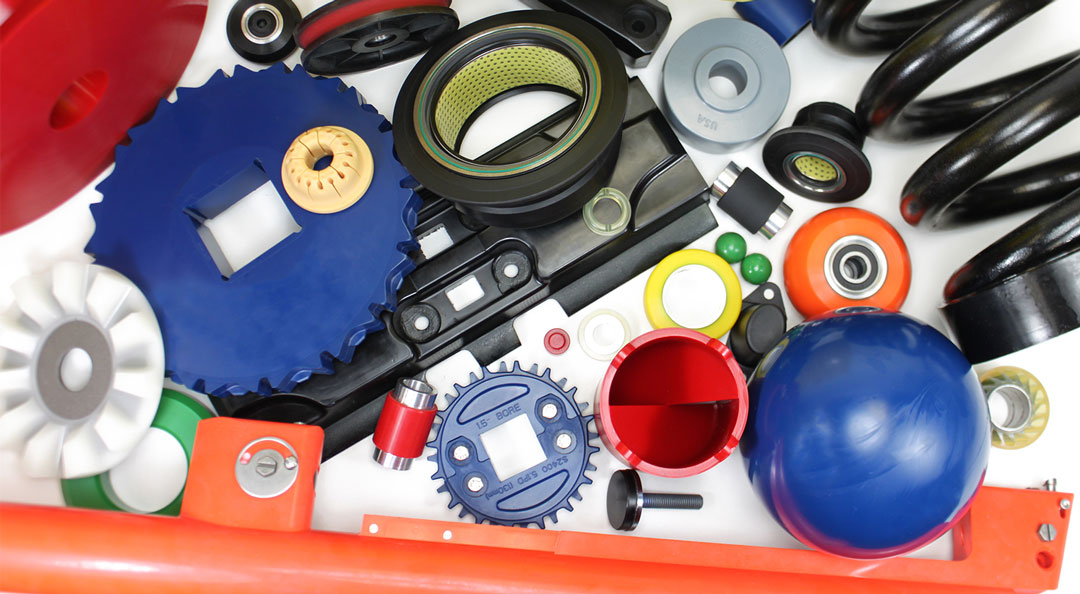
Case in Point: the John Deere Cotton Doffer
The doffer is one of two critical components that work together to pick cotton. First, barbed spindles rotate at high speed to remove the seed-cotton from the plant. Then, counter-rotating doffers pull the seed-cotton off of the spindles. It is a tough job subject to abrasive field conditions.
The problem John Deere faced was two-fold. First, the rubber doffers wore too quickly. Second, the black fragments that wore off the rubber doffers contaminated the white cotton harvest.
We worked with John Deere to understand the doffer application. Then we went to work on a custom polyurethane formulation to match their requirements. There were prototypes, field tests, and more prototypes. In the end, we significantly improved doffer wear life and eliminated the black rubber contamination. Our polyurethane doffer has been the industry standard for the past 30 years.
But it’s not about us. We’re happy to have made a contribution to John Deere’s market leadership.